In the manufacture
of the KD woven corrugator belt, textile engineers, with strength
and hygroscopic properties in mind, carefully select natural cotton
fibers for the inner ply. Only extremely high grade heat and wear
resistant polyester fibers are used for the two outer plies.
The three
(3) ply belts are woven on sophisticated computer controlled looms that
monitor the welt and the weave throughout production. Experienced
textile engineers exercise strict supervision and do the QC managers.
Precise
pre-stretching and thermofixing (heat setting) follow the completion of
weaving. These technically delicate procedures prevent stretching in the
corrugating line, and insure that the dimensional stability of the belt
remains well less than 1% during the life of the belt.
As the
belt does not stretch, there
is no need of over tension to keep it running true. Only enough tension
is applied to establish traction between belt and paper. Lower tension
contributes to less machine wear, less maintenance and less power
consumption.
After the
belt is cut to size, the ends are honed to create a "setback"
in preparation for lacing. The setback insures that the #6 stainless
steel laces are crimped into the belt so that they are below the surface
line of the joined belt. High heat resistant silicone is then applied
and smoothed over the lacing, covering it to aid in avoiding marking.
The lacing is crimped into the belt, not compressed or heated thereby
weakening the material.
The KD
belt is guaranteed to perform at least as long as any previously used
belt, because it is: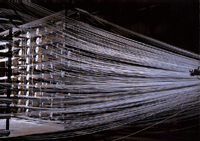
A. More durable.
B. Tracks perfectly.
C. Runs with less tension.
D. It is the easiest of ANY belt to clean.
The KD
belt is priced to be competitive and commands the best performance ratio
per dollar cost (million square feet board - $)
|